Allgemeine Konstruktionshinweise
Reibung
IDG-Werkstoffe basieren vorwiegend auf Compounds, die auf einer Matrix aus Polytetrafluorethylen (PTFE) aufgebaut sind und dadurch eine sehr geringe Haft- bzw. Anfahrreibung aufweisen.
Dies begründet sich darin, dass reines PTFE einen niedrigen Reibbeiwert hat, der unter Belastung noch sinkt.
Weitere Faktoren beeinflussen den Reibbeiwert. Unter anderem der Werkstoff der Gegenlauffläche, dessen Rautiefe und Härte, die Gleitgeschwindigkeit sowie Temperatur und die Schmierung.
IDG-Werkstoffe auf PTFE-Basis zeichnen sich durch ratterfreies Gleitverhalten aus.
Einfluss der Gegenlauffläche
Die Rautiefe und Formtreue der Gegenlauffläche beeinflusst sehr stark Leckageentwicklung und Lebensdauer. Oberflächen mit möglichst hohem Traganteil sind anzustreben. Dies wird durch Feinstschleifen, Honen und Läppen erreicht. Dabei werden auch Rauspitzen und Porenkanten entschärft. Letzteres ist besonders bei harten Gegenlaufflächen von großer Bedeutung!
Eine durch Rollieren oder Glattwalzen erzielte Glättung der Oberfläche kann ungleichmäßig und wellig ausfallen, was sich auf Dichtungen aus hochleistungsfähigen Kunststoff-Compounds besonders nachteilig auswirkt.
Für Dreh- und Schwenkbewegung muss die Gegenlauffläche drallfrei im Einstechverfahren geschliffen sein.
Oberflächenrauheit, Materialanteil
Oberflächenrauheit nach DIN EN ISO 4287
Dichtung und Gegenlauffläche sind immer als Paarung zu betrachten. Die Funktionssicherheit und Lebensdauer einer Dichtung ist daher im wesentlichen von der Oberflächenbeschaffenheit der Gegenlauffläche abhängig.
Kratzer, Riefen, Lunker, konzentrische oder spiralförmige Bearbeitungsriefen sind nicht akzeptabel. Grundsätzlich sind an die Gegenlaufflächen bei dynamischen Anwendungen höhere Ansprüche zu stellen als bei statischen Applikationen.
Die zur Beschreibung der Oberflächenfeingestaltung am meisten angewandten Kenngrößen (Rz, Rt und Ra) sind in der DIN EN ISO 4287 definiert. Da diese Größen in manchen Fällen alleine nicht ausreichend sind, sollte der Materialanteil (Rmr) festgelegt werden.
Der Materialanteil (Rmr) ist maßgebend um Oberflächen zu bewerten, da diese Kenngröße von der jeweiligen Profilform bestimmt wird. Diese wiederum ist das Ergebnis des jeweiligen Bearbeitungsverfahrens.
Oberflächenprofile
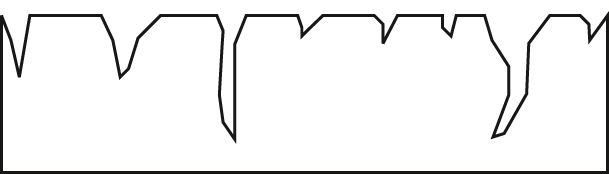
Ra 0,1 | Rz 1,0 | Rmr 70 %
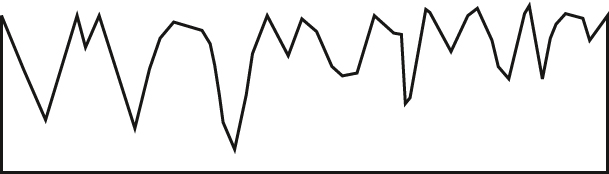
Ra 0,2 | Rz 1,0 | Rmr 15 %
Die Grafik zeigt, dass die Angaben Ra und Rz die Profilform nicht ausreichend beschreiben und damit eine Beurteilung der Oberfläche zur Eignung für die Dichtungstechnik nur ungenügend ist.
Schutz vor hydrodynamischem Schleppdruck
Bei Linearführungen mit engem Spalt zwischen ruhendem Gehäuse und bewegter Fläche, baut sich durch Längsbewegung im Medium eine hydrodynamische Schleppströmung auf. Wird diese durch eine Dichtung ‘gestoppt‘, kommt es zu einer Druckerhöhung, die insbesondere bei ‘langen‘ Bewegungen den Systemdruck um ein Mehrfaches überschreiten kann.
Deshalb sollte der Raum vor der Dichtung möglichst großvolumig ausgeführt werden.
Reicht dies nicht aus, ist ein Rücklaufkanal (als Spiralnut) oder die Anwendung von MANOY® Führungsringen mit Schrägschlitz bzw. Führungsbändern vorzusehen. Damit wird der kritische Druckaufbau vor der Dichtung vermieden.
Nachglätten, Einlaufen
Die Gegenlauffläche wird während der Einlaufzeit durch die Dichtungs- und Führungselemente nachgeglättet.
Allerdings fördern kurze Hübe in rascher Folge und oszillierende Bewegungen die Bildung unerwünschter Laufspuren. Fremdschwingungen, die von einer anderen Stelle der Konstruktion herrühren, erzeugen dieselbe Wirkung. Um das unerwünschte Einlaufen möglichst auszuschließen, sollte die Gegenlauffläche hart sein.
Härte der Gegenlauffläche
Generell ist der Verschleiß von Dichtungselementen auf harten Gegenlaufflächen geringer als auf weichen Werkstoffoberflächen. Insbesondere bei rotativen Anwendungen besteht die Gefahr des Einlaufens durch Spurrillenbildung.
Sind die Gegenlaufflächen ungenügend hart, können zudem Verschmutzungs-Kratzer zu Beschädigungen der Dichtungs- und Führungselemente führen. In der Konsequenz führt dies über kurz oder lang zu einer Leckage.
Die Mindesthärte sollte bei linearer Bewegung über 58 HRC bzw. bei rotativer Anwendung über 62 HRC liegen.
Rahmenbedingungen
Die Einführschrägen an Stangen, Wellen und Bohrungen müssen entsprechend der Darstellung der jeweiligen Einbausituation bei den verschiedenen Dichtungen vorgesehen werden.
Dicht- und Abstreifelemente aus Kunststoffen und Elastomeren dürfen nicht über scharfe Kanten, Gewindespitzen, Querbohrungen, Nuten und raue Flächen geschoben werden. Dies sollte unbedingt schon bei der Auslegung beziehungsweise bei der Konstruktion berücksichtigt werden.
Falls dies nicht berücksichtigt wurde, müssen diese Stellen für die Montage abgedeckt werden.
Führen, Zentrieren
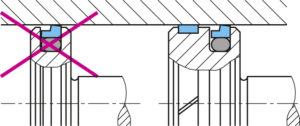
Der metallische Kontakt zwischen Kolben, Stange und Gehäuse muss verhindert werden. Durch Anlaufen entstehende Riefen würden Dichtung, Führung und Abstreifer beschädigen und zu Leckage führen.
Weder Dichtung noch Abstreifer eignen sich für Führungsaufgaben. Dafür sind separate Führungselemente mit ausreichender Tragfähigkeit vorzusehen.
Schmierung, Trockenlauf
Fast alle IDG-Werkstoffe auf PTFE-Basis sind trockenlauffähig. Trockenlauf mindert jedoch die Standzeit des Systems Dichtung/Gegenlauffläche.
Bei einem geschlossenen Schmierfilm im Dichtspalt reduziert sich der Reibbeiwert. Bei Hydraulik- oder Schmieröl ergibt sich der geringste Reibbeiwert.
Außerdem senkt ein Schmierfilm die Wärmeentwicklung im Dichtspalt und erhöht die Standzeit.
Bei Anwendungen wie Pneumatikzylindern und Führungsstangen genügt in der Regel eine einmalige Montageschmierung.
Abrasivpartikel im Medium
Partikel sind in der Regel nicht die Ursache für eine Leckage, sorgen aber für erheblichen Verschleiß des Systems Dichtung/Gegenlauffläche und somit zum vorzeitigen Ausfall der Dichtung. Für den Verschleiß eines Systems sind nicht nur die Größe, sondern auch die Anzahl abrasiver Schwebstoffe maßgebend.
Bei einer typischen Schmierfilmdicke von 0,5 μm schwimmen kleine Partikel durch, größere führen zu einem Verschleiß an Dichtungen und Gegenlauffläche.
Durch konstruktive Maßnahmen (z. B. Filtertechnik) sollte die Anzahl der Partikel gering gehalten werden. Maßgebend für die Qualifizierung und Quantifizierung der Medienreinheit sind die Normen ISO 4406 und NAS 1638.