Function of a plastic seal
Basic structure
Plastic seals normally consist of two components.
The sealing ring is generally made from a wearresistant PTFE compound. This material is so efficient that these seals can meet the highest pressure, speed and temperature resistance specifications. Since the maximum values are each based on different compounds, preliminary trials are essential to achieve the objective on special requirements.
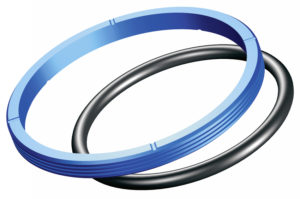
An elastic energizer is used to press the sealing edge or sealing surface firmly against the mating surface. This squeeze guarantees continual sealing. An elastomeric precision O-ring or profiled steel spring is used to generate this squeeze. O-rings also act as a static seal in the base of the groove.
All the service conditions must be considered when selecting the material for the sealing ring and energizer.
Inner or outer sealing
All radially acting seals are manufactured in inner or outer sealing versions.
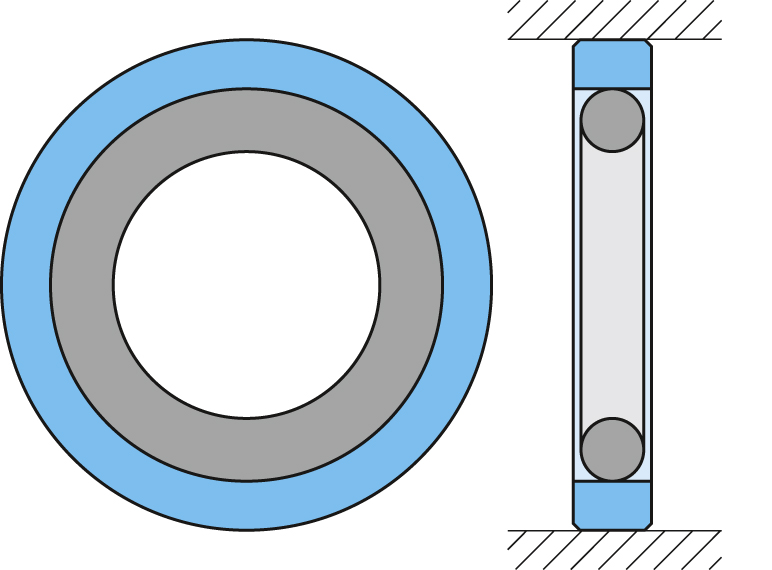
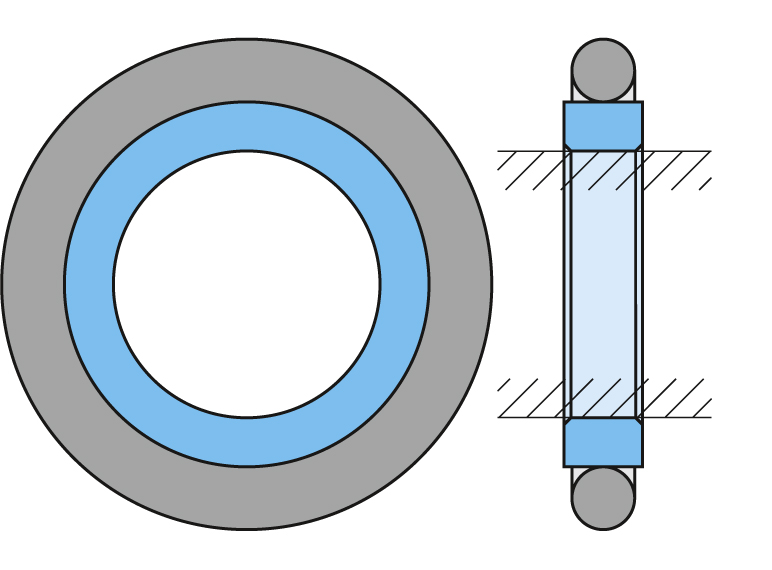
Generation of sealing force
MANOY® sliding rings and MANOY® U-Cups are pressure-activated sealing systems. The elastic precision O-ring when compressed acts as a static seal in the base of the groove and presses the dynamic sealing element against the mating surface.
When the O-ring is pressurized by the medium it functions like an incompressible high viscous fluid by applying its sealing force on the surrounding surfaces.
Up to about 2 MPa the sealing effect is produced almost entirely by the compressive force of the energizer.
Profile design
The different profile designs of the sealing rings are largely determined by the type of motion, the direction of pressure application, the level of pressure and the fluid to be sealed.
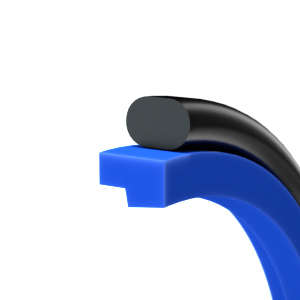
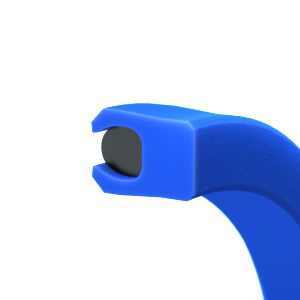
Precision O-ring squeeze
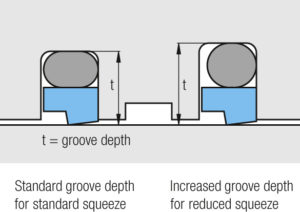
To ensure a good seal, the housings are designed so that medium squeeze is produced by the precision O-ring or a profiled spring energizer.
A smaller groove depth produces higher compression and therefore improves the sealing effect at low pressure (up to about 2 MPa) and in unpressurized operation.
A larger groove depth produces smooth running but to the detriment of seal tightness.
Clearance gap
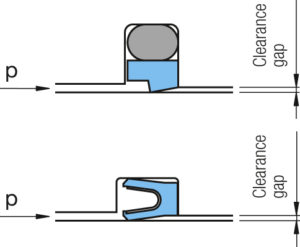
The minimum clearance gap required is dependent on the bearing accuracy and the other design constraints. Pressure expansion and thermal expansion must also be taken into account.
The clearance gap should be as small as possible on the side not under pressure. On the side under pressure, a greater clearance gap can prevent particles sticking.
At pressures of over 40 MPa, minimum fits of H8/f8 for the bore/piston diameters and/or the casing/rod diameters should be maintained.
If the clearance gap is too large on the side not under pressure, the sealing element extrudes into the gap and is destroyed.
Seal cross-section and total tolerance range
If it is impossible to accommodate a recess for the housing, the specified upper limit for a diameter range may possibly be exceeded.
It should be remembered that the smaller the sealing cross-section selected, the smaller the total seal-relevant tolerances must be.
Therefore the objective should be a seal cross-section which is as large as possible.
Sealing
An absolutely tight seal can only be achieved with static seals and not with dynamic seals. Nor would this be desirable, as complete dryness would cause high wear on the sealing elements. The aim is to leave a very thin, dry looking lubricating film on the mating surface.